Injection Molding Automotive Parts: Revolutionizing the Automotive Industry
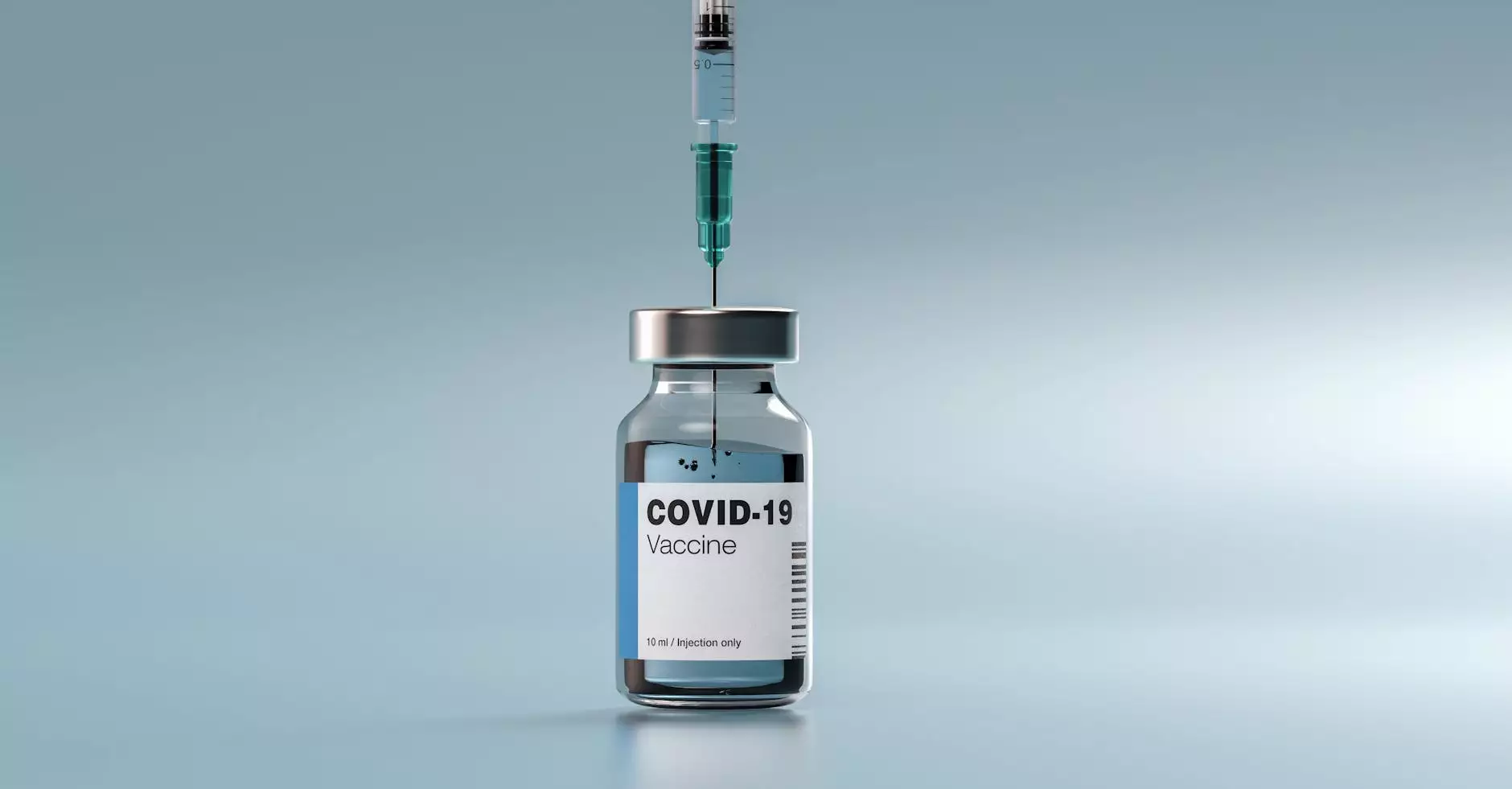
The automotive industry has undergone significant transformations over the past few decades, with technological advancements paving the way for efficiency, quality, and sustainability. One of the key processes driving this evolution is injection molding automotive parts. This manufacturing technique, known for its precision and versatility, has become indispensable in producing a wide array of high-quality components for vehicles. In this article, we will delve into the multifaceted world of injection molding automotive parts, exploring its benefits, applications, and the future outlook for this vital technology.
Understanding Injection Molding
Injection molding is a manufacturing process where material is heated until it becomes molten and is then injected into a mold cavity under high pressure. This method is not only applicable to plastics but can also be used for metals and other materials. The process is characterized by its ability to produce complex shapes with exceptional dimensional accuracy and repeatability. The typical injection molding process includes:
- Material Selection: Choosing the right material, often thermoplastics for automotive parts.
- Heating: The selected material is heated to a molten state.
- Injection: The molten material is injected into a mold under high pressure.
- Cooling: The material cools and solidifies, taking the shape of the mold.
- Demolding: The solidified part is ejected from the mold.
The Advantages of Injection Molding in Automotive Parts Production
Injection molding offers numerous advantages that make it the preferred method for manufacturing automotive components. Here are several key benefits:
1. Efficiency and Speed
One of the foremost advantages is the speed of production. Injection molding can produce high volumes of parts in a relatively short time. The ability to automate the process allows manufacturers to significantly reduce cycle times, leading to overall cost savings.
2. Precision and Quality
Injection molding is renowned for its ability to create parts with high precision and uniform quality. The molds can be engineered to tight tolerances, which ensures that the parts consistently meet the necessary specifications crucial for vehicle safety and performance.
3. Design Flexibility
This process provides considerable design flexibility, allowing for the production of complex geometries that are often difficult or impossible to achieve through other manufacturing methods. As a result, designers have the freedom to innovate, enhancing the functionality and aesthetics of automotive components.
4. Material Versatility
Injection molding accommodates a wide variety of materials, including various thermoplastics, thermosetting plastics, and even some metals. This versatility enables automotive manufacturers to select materials that provide unique properties such as lightweight, strength, and durability.
5. Sustainable Manufacturing
With an increasing focus on sustainability, injection molding processes have adapted to meet these demands. The ability to recycle materials and minimize waste through precise material usage has made it an environmentally friendly option in automotive part manufacturing.
Applications of Injection Molding in the Automotive Sector
Injection molding is used to manufacture a wide range of automotive parts, some of which include:
- Dashboard Components: Complex shapes with integrated features such as air vents and infotainment systems.
- Exterior Trim: Parts such as grilles, bumpers, and moldings that require both strength and aesthetic appeal.
- Interior Panels: Molded components that provide functionality and style inside the vehicle.
- Under-the-Hood Parts: Heat-resistant components that withstand the rigorous conditions of an engine compartment.
- Electrical Housings: Protective casings for electrical systems that ensure safety and reliability.
Case Studies: Success Stories of Injection Molding in Automotive Parts
Several automotive manufacturers have successfully integrated injection molding into their production processes, leading to remarkable outcomes. Here are a few case studies:
1. Ford Motor Company
Ford has leveraged injection molding for its Focus and Fiesta models, enhancing production efficiency and reducing material waste. By adopting advanced mold designs, Ford was able to create complex, lightweight components that improved vehicle performance while adhering to stringent safety standards.
2. General Motors
General Motors utilized injection molded components for its Chevrolet Silverado. Utilizing recycled materials, GM enhanced the sustainability of its production while maintaining its vehicles' performance and design integrity. This move not only reduced costs but also aligned with environmental responsibility initiatives.
3. Toyota
In their Prius line, Toyota has employed injection molding to produce parts that contribute to overall vehicle light-weighting. This has been instrumental in improving fuel efficiency and reducing emissions, reinforcing Toyota's commitment to sustainability while delivering reliable performance.
The Future of Injection Molding in Automotive Parts
The future of injection molding in the automotive industry appears promising, driven by ongoing technological advancements and changing consumer demands. Here are several trends shaping this future:
1. Advancements in Materials
The continuous development of new materials, including bio-based plastics and composites, will broaden the scope of what can be achieved through injection molding. These innovations will enhance the properties of automotive parts, providing improved durability, weight savings, and environmental benefits.
2. Smart Manufacturing Integration
As industry 4.0 takes shape, the integration of smart manufacturing technologies, including IoT, automation, and data analytics, will optimize injection molding processes. Real-time monitoring and predictive maintenance will improve efficiency and reduce downtime, leading to enhanced production capabilities.
3. Sustainability Focus
As consumers become more eco-conscious, the automotive industry will need to focus on sustainable practices. Injection molding will play a pivotal role in this shift, with recycling and waste reduction efforts at the forefront. Manufacturers are likely to increasingly adopt closed-loop systems that reclaim scrap material, promoting a circular economy.
Conclusion
In conclusion, injection molding automotive parts is not just a manufacturing technique; it is a driving force behind the evolution of the automotive industry. The advantages of efficiency, precision, cost-effectiveness, and sustainability make it an essential part of automotive manufacturing. As we move forward, the continual improvements in technology and material science will further enhance the significance of injection molding, ensuring that it remains at the forefront of automotive innovation and production. Companies like DeepMould are well-positioned to lead the way in this dynamic landscape, offering cutting-edge solutions in metal fabricators, and setting the standard for quality and efficiency in the industry.